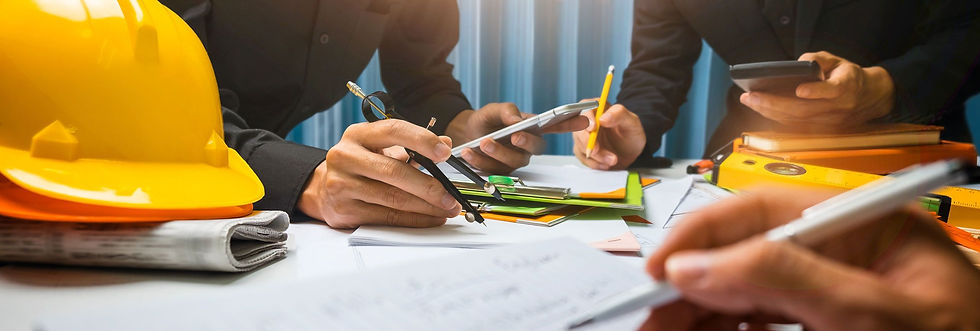
ADVANCED ENGINEERING
Learn about the components of the Simeken PRO™ System.
Simeken PRO™: Advanced Waste Treatment
The PRO™ System (Pyrolysis Recovery Oven) is a high-temperature thermal device that can reduce waste, provide recycled by-products, and create heat for the generation of clean electricity and renewable fuels with its advanced waste treatment technology. Our System operates in an oxygen-restricted environment to help eliminate air pollution by creating none of - or very little of - the many pollutants found in incineration or other proposed pyrolysis methods. Capable of processing anywhere from 50 to 200 tons of waste material a day, the PRO™ System can generate 4 to 60 megawatts of power through the use of a cogeneration system.
The PRO™ process applies high temperatures (from 1200°F to 1600°F) indirectly to a retort chamber which houses an environment free of flame and oxygen. Inside this oven, hydrocarbons and other waste components are converted into gases and basic elemental solids through destructive
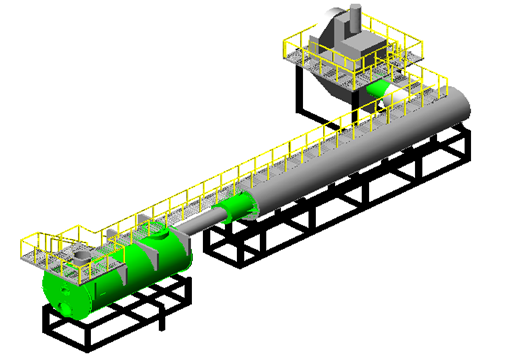
distillation and molecular decomposition. All the off-gases are diverted to a thermal oxidizer operating above 2000°F for conversion to carbon dioxide, oxygen and water vapour. The remaining solid residues are typically carbon, sterile sands, and fixed, non-leachable metals.
In addition to destroying waste materials, the PRO™ System facilitates the cost-effective use of all processing by-products. For example, the heat from the thermal oxidizer can be routed to waste-heat boilers to produce process steam or electricity via steam cogeneration units. Solid residues, depending on the nature of the input, can often be recycled, sold as commodities (biochar), or formed into construction material.
This technology serves dual purposes by helping to address the growing worldwide problem of waste disposal, while utilizing the waste product to generate energy in the form of electricity for the surrounding communities or green fuels to reduce our carbon footprint. It has been approved in Mexico, and is pending approval by San Joaquin Valley Air Pollution Control District as well as other agencies in the USA for air quality.
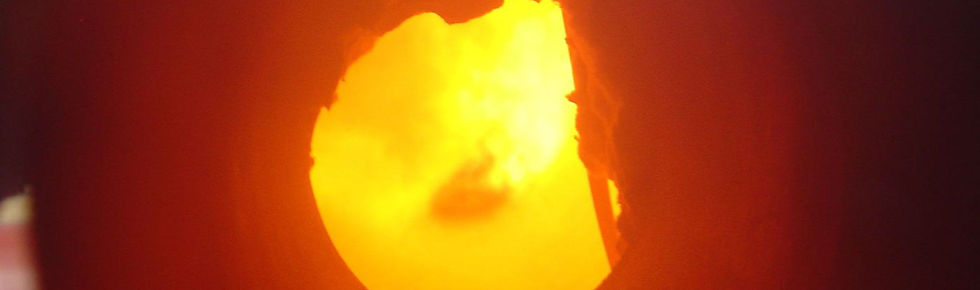
GASIFICATION PROCESS
The Hybrid Gasification Unit, entitled the PRO™ System, uses an advanced pyrolytic technology to thermally convert almost any carbon-containing compound into hydrocarbon vapour and carbon char. The hydrocarbon vapour can be either used directly to produce heat energy or condensed and processed into a valuable hydrocarbon liquid. The marketable carbon char (biochar) is also recovered.
The PRO™ System in its basic configuration consists of five components:
1. The Shredding and Conveying System
2. The PRO Retort Oven
3. The Thermal Oxidizer
4. The Wet Scrubber
5. The Char Output System
Please refer to the Material Flow Diagram for a clear understanding of the PRO™ System process.
1. The Shredding and Conveying System
The Shredding and Conveying System consists of a shredder/grinder mechanism designed for the primary waste stream input(s) of the system, which can include virtually any organic material, such as:
- Wood, construction and demolition waste
- Scrap tires
- Sewage sludge
- Animal and other organic waste
- Petro-chemical waste
- Medical and bio-hazard waste
- Municipal solid waste
The shredded waste stream materials are transported by conveyor to the top of the PRO™ System.
2. The PRO™ Retort Oven
The PRO™ Retort Oven consists of a thermal converter that conveys the input stream (tires, scrap wood, medical waste, and agricultural waste - nearly anything organic) through an oxygen-depleted environment via sinusoidal waves and gravity. Because of the low oxygen, most of the harmful gases generally associated with combustion are not produced. The thermal converter is a thermal combustion chamber that can reach temperatures as high as 1600°F, which creates an environment where all the materials entering the oven are deconstructed into basic hydrocarbon vapour and carbon char. This process, in which the hydrocarbon vapours are created, is the primary reason why the PRO™ operates so cleanly.
Once the material has reached its resonance time and temperature, the remaining material is carbon char (biochar). A cooling system at the end of the retort cools the carbon char as it drops from the thermal converter. (The cooling system can also be designed as a water distillation process where contaminated water is treated to have an end result of purified water.)
The final output is carbon char (biochar) and liberated hydrocarbon gases (syngas). The hydrocarbon gases are then treated through a thermal oxidizer to produce energy, and a wet scrubber to meet with environmental emission regulations or further refined to create high-revenue renewable fuels such as hydrogen and natural gas.
3. The Thermal Oxidizer
The Thermal Oxidizer introduces air (oxygen) into the combustion chamber to process the remaining gases from the oven. The retort exhaust gases are combusted and superheated to temperatures as high as 2000°F, but generally in the range of 1600°F to 1800°F. This intense heat energy can then be harnessed and used to create steam and spin turbines for the clean generation of electricity.
4. The Wet Scrubber
The Wet Scrubber is part of the reason why the PRO™ System has such clean emissions. This unit is basically a clean air device, which forces the exhaust gases into a spray chamber. There, the gases come into intimate contact with an aqueous sodium hydroxide medium which removes any remaining particulate material contained in the gas stream and neutralizes many unfavorable gases. The Wet Scrubber also contains a dewatering system to prevent any entrained water from leaving through the stack.
5.The Char Output System
The Char Output System removes the recyclable output from the bottom of the oven. Although the precise composition of this material depends on the waste input, it is generally a pure carbon char (biochar) that can be profitably sold, or further refined into products such as activated carbon.

PROVEN SOLUTION
Our 75 ton per day system was installed in Matamoras, Mexico in November, 2004 and was tested using some of the largest polluters in the area - used tires, wood waste, and sewage sludge. With the assistance of the city of Matamoras, this location allowed us to test local wastes to make sure that the PRO™ unit will work as advertised, and will provide the quality of output and reliability needed to support this technology in the long term. Based on our findings and economic projections, our new machines are designed and manufactured with the capacity of 150 tons per day. At these rates of production, the PRO™ System will provide an excellent return on investment as well as the production of very clean energy and valuable, marketable outputs. A second unit has been built in California.
The true advantage of this technology is the design of the PRO™ System. Most pyrolysis systems in the past were plagued with reliability issues. The PRO™ System uses a "free fall" action for movement that is assisted by sinusoidal action. The bottom line is that there are no moving parts inside of the oven, dramatically improving the reliability of the entire system.
Why the Simeken PRO™ System Is Better:
- Many waste streams
- Low emissions
- Pure carbon output (biochar)
- Safety and reliability
- Competitive comparison

MANY WASTE STREAMS
Virtually any organic material can be fed into a Simeken PRO™. We can design foolproof feed systems that will work with, for example:
Agriculture
Plastics industry waste
Medical waste
Tires
Wood industry waste
Contaminated soils
Municipal solid waste
Paper & pulp industry waste
Biomass
Construction & demolition debris
Sewage sludge
Hazardous waste
Food industry waste
Farm by-products
Want more specifics?
Here's a list of contaminants that we have successfully destroyed, in our pilot 2.5 ton per day plant:
Acetone
Acetonitrile
Aldicarb
Benzene
BOD
Butric acid
Carbon tetrachloride
Chlorobenzene
Chloroform
Chloropheol
Cloracetic acid
COD
Color
Cyanide compounds
Cyclohexane
Cyclohexanone
Dibutyl phthalate
Dichlorobenzene
Dichloroethane
Dichloroethylene
Dichloro pentadiene
Dichlorophenoxy-acetic acid
Dichlorotriflourethane
Dimethylbutane
Dithane
Ethanol
Ethylcyclobutane
Ethylenediaminetetracetic acid
Ethylene dibromide
Formaldehyde
Formic acid
Freon-TF
Hexachlorobutadiene
Hexachloroethane
Hydrazine
Isopropanol
Methylcyclopentane
Methylene chloride
Methlethylketone
MethyI isobutyl ketone
Methylpentane
n-Butylamine
Naphthalene
Pentachlorophenol
Pentane
Phenol
Polychlorinated biphenyl
PCBs
Resorcinol
Sodium thiocyanate
Sulfolane
Tetrachloroethane
Tetrachloroethylene
Tetrachlorophenol
Tetrahydrofuran
TOC
Toluene
Trichlorobenzene
Trichloroethane
Vinyl chloride
Xylene
Whatever your needs are, contact us today to determine how we can help you.
We’ll custom design a solution for you.

LOW EMISSIONS
The Simeken PRO™ quickly and cleanly deconstructs all organic input matter into basic hydrocarbon vapour and carbon char, in an oxygen-reduced environment designed to avoid adverse chemical reactions. This ensures that we begin with the minimum of unwanted gas that needs to be removed. The hydrocarbon gases then pass through a thermal oxidizer, where they are superheated to temperatures in excess of 1600°F to produce energy. This extremely high heat allows for a complete combustion of the gases.
Finally, a wet scrubber forces the exhaust gases into a spray chamber. There, the gases come into contact with an aqueous sodium hydroxide medium which removes any remaining particulate material contained in the gas stream and neutralizes many unfavorable gases to surpass environmental emission regulations.
Our trial emission results detail just how clean the emissions really are. Breathe a sigh of relief!

BIOCHAR: PURE CARBON OUTPUT
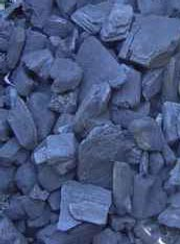
Although the precise composition of the solid char material (also known as biochar or carbon char) output from the Simeken PRO™ System depends on the waste input, it is generally a pure carbon char that can be profitably sold, burned for energy, or further refined into products such as activated carbon fertilizer.
Biochar is very useful since it ameliorates the soil texture and releases fertilizer slowly. It aids in nutrient retention and promotes healthy root growth, while minimizing pathogens that cause both diseases and bugs. When compared to chemical fertilizers, biochar contains oligo-elements, such as selenium, which help achieve higher crop yields. When compared to other "natural" fertilizers such as manure or sewage, it is safer since it has been disinfected at high temperature and, being a solid, greatly reduces any risk of water table contamination. Pyrolytic char is thought to be a major component in the formation of ancient terra preta soils. Efforts are underway to recreate these soils through
the production of biochar, which is designed to promote nutrient retention and enhance soil ecology.
Biochar also holds great promise for carbon sequestration in the mitigation of global warming. To put it simply, the carbon that becomes locked into the carbon char output from the Simeken PRO™ System reduces the amount of free carbon in the world, and thereby also reduces the amount of global warming.
To show the purity of the carbon char from the Simeken Pro, we engaged CRT Laboratories to analyze samples. CRT is UL Approved-Registered / ISO 9002 Certified and ISO-IEC 17025 Certified, along with an update to ISO 9001:2000.

SAFETY AND RELIABILITY
Our first pyrolysis research and development demonstration unit tested multiple contaminants. This 75 tonne per day (tpd) unit was extensively tested for eleven months by Simeken at a demonstration site in Matamoros, Mexico. A second unit is now operating in Bakersfield, California.
The true advantage of this technology is the design of the PRO™ System. Most pyrolysis systems in the past were plagued with reliability issues. The PRO™ System uses a "free fall" action for movement that is assisted by sinusoidal action. The bottom line is that there are no moving parts inside of the oven, dramatically improving the reliability of this system.
We design plants with a 24/7 operation in mind. Our simple design with no moving parts in our retort and oxidizer eliminate key service issues. Our plants are monitored via the internet with self-correction feedback, safety and shut-down features. We incorporate redundant controls to maximize safety and prevent problems.
Simeken has developed its own proprietary systems for the management and operation of the system. This software and hardware configuration can be monitored and adapted remotely providing accurate reporting and status of each installation. This system management system:
-
Controls all mechanical operations of the machine
-
Controls system overrides that keep the machine in operating tolerances
-
Enacts safety backup systems to provide a safe working environment
-
Provides statistics, performance, and emissions data "real time" to effective monitoring
Although Simeken offers industry-standard representations and warranties, we have designed our system for an extended lifespan that meets and surpasses industrial averages by incorporating the best materials of construction.

COMPETITIVE COMPARISON
There are other pyrolytic systems in development, but very few are near commercialization. The other technologies and their approaches were reviewed in the early work of our system. They were found to still produce carcinogenic components in the waste gas, by-products in the waste stream, and very corrosive refuse-derived fuel, which is why these other pyrolysis systems have not been commercialized. Unlike our Simeken PRO™ System's technology, which has been commercially tested, other pyrolysis systems' lack of commercial experience means that most of the processes still present some risk to the potential owner. These risks could cause higher capital or operating costs, lower reliability, and/or lower energy recovery efficiency.
Burning wastes through incineration with direct flame in the presence of oxygen can be explosive, causing turbulence in the burn-chamber and fostering a recombination of released gases. Waste destruction in an oxygen-rich atmosphere makes conversion far less complete, is highly inefficient and creates harmful substances. Pyrolysis, known for hundreds of years, is the solution. Unlike incineration, the singular advantage of pyrolysis (the technology behind the PRO™ System) is the destructive decomposition of waste materials using indirect heat in the absence of oxygen.
Microwave-based technology has been used in the destruction of tires, but has been found to produce carcinogenic residuals in its output products. Our Simeken PRO™ System does not produce any carcinogenic by-products or radiation, and can handle tires as well as solid and liquid waste streams.
Waste-to-energy incineration systems produce a high level of fly ash, dioxins and furans. As our trial results clearly demonstrate, the Simeken PRO™ System produces very minimal pollutants.
Micro/biologic destruction technologies, or engineered microbes, have a limited application, but are appropriate for the cleanup of some intractable waste problems and yield environmentally acceptable results; however, they work on limited forms of waste, and are very time-consuming. The PRO™ System can process many waste streams. Specialized processing lines can be engineered to treat industrial waste, PCBs, medical wastes, petrochemical wastes, municipal solid wastes and a wide variety of other waste materials.
Landfill solutions are becoming less and less attractive. Landfill sites are hard to get approved due to the inherent problems, such as leaking of toxic products into adjacent groundwater supplies. Existing landfills sites are rapidly reaching capacity, so municipal waste has to be shipped farther and farther to new landfill sites, increasing costs dramatically in many markets. The PRO™ System can provide up to 90% volume reduction of many feed materials.
Contact us to better understand how our PRO™ System can be useful to you.